Especificación para API de envoltura e tubería Especificación 5CT Ninth Edition-2012
Estándar: API 5CT | Aliaxe ou non: non |
Grupo de grao: J55, K55, N80, L80, P110, etc. | Aplicación: tubo de aceite e carcasa |
Grosor: 1 - 100 mm | Tratamento de superficie: como requisito do cliente |
Diámetro exterior (redonda): 10 - 1000 mm | Técnica: enrolado en quente |
Lonxitude: R1, R2, R3 | Tratamento térmico: calmar e normalizar |
Forma da sección: rolda | Tubo especial: articulación curta |
Lugar de orixe: China | Uso: aceitado e gas |
Certificación: ISO9001: 2008 | Proba: NDT |
Tubo dentroAPI5CTúsase principalmente para a perforación de pozos de petróleo e gas e o transporte de petróleo e gas. A carcasa de aceite úsase principalmente para soportar a parede do buraco durante e despois da finalización do pozo para garantir o funcionamento normal do pozo e a finalización do pozo.
Grao: J55, K55, N80, L80, P110, etc.
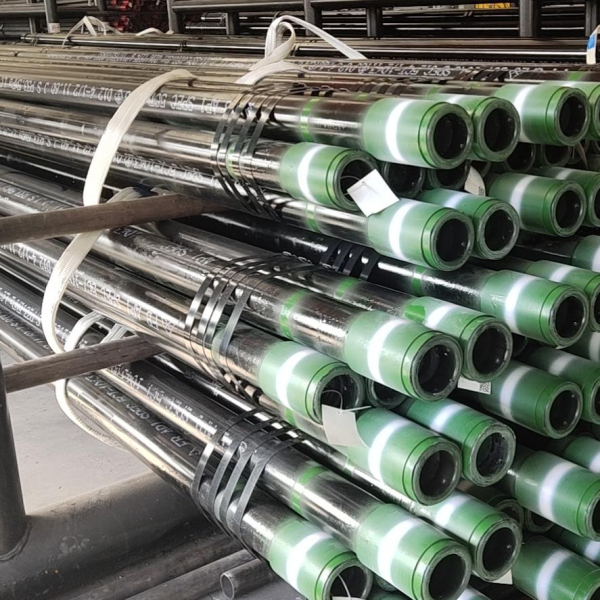
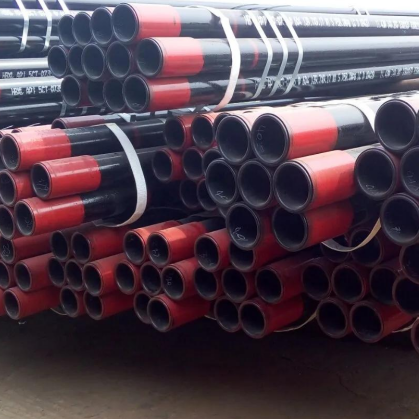
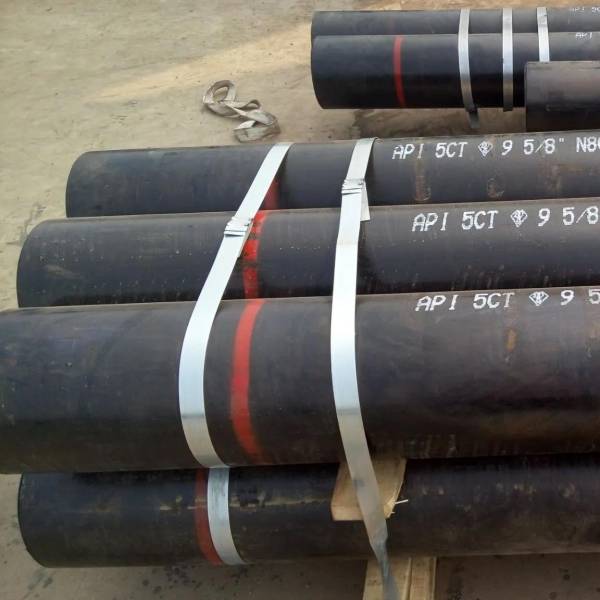
Grao | Tipo | C | Mn | Mo | Cr | Ni | Cu | P | s | Si | ||||
min | máx | min | máx | min | máx | min | máx | máx | máx | máx | máx | máx | ||
1 | 2 | 3 | 4 | 5 | 6 | 7 | 8 | 9 | 10 | 11 | 12 | 13 | 14 | 15 |
H40 | - | - | - | - | - | - | - | - | - | - | - | - | 0,03 | - |
J55 | - | - | - | - | - | - | - | - | - | - | - | - | 0,03 | - |
K55 | - | - | - | - | - | - | - | - | - | - | - | - | 0,03 | - |
N80 | 1 | - | - | - | - | - | - | - | - | - | - | 0,03 | 0,03 | - |
N80 | Q | - | - | - | - | - | - | - | - | - | - | 0,03 | 0,03 | - |
R95 | - | - | 0,45 c | - | 1.9 | - | - | - | - | - | - | 0,03 | 0,03 | 0,45 |
L80 | 1 | - | 0,43 a | - | 1.9 | - | - | - | - | 0,25 | 0,35 | 0,03 | 0,03 | 0,45 |
L80 | 9cr | - | 0,15 | 0,3 | 0,6 | 0 90 | 1.1 | 8 | 10 | 0,5 | 0,25 | 0,02 | 0,03 | 1 |
L80 | 13cr | 0,15 | 0,22 | 0,25 | 1 | - | - | 12 | 14 | 0,5 | 0,25 | 0,02 | 0,03 | 1 |
C90 | 1 | - | 0,35 | - | 1.2 | 0,25 b | 0,85 | - | 1.5 | 0,99 | - | 0,02 | 0,03 | - |
T95 | 1 | - | 0,35 | - | 1.2 | 0,25 b | 0,85 | 0 40 | 1.5 | 0,99 | - | 0 020 | 0,01 | - |
C110 | - | - | 0,35 | - | 1.2 | 0,25 | 1 | 0,4 | 1.5 | 0,99 | - | 0,02 | 0,005 | - |
P1I0 | e | - | 一 | - | - | - | - | - | - | - | - | 0,030 e | 0,030 e | - |
Qi25 | 1 | - | 0,35 | 1.35 | - | 0,85 | - | 1.5 | 0,99 | - | 0,02 | 0,01 | - | |
Nota Os elementos mostrados deberán informarse na análise do produto | ||||||||||||||
A O contido de carbono para L80 pode incrementarse ata un 0,50% máximo se o produto está recollido polo aceite ou o polímero. | ||||||||||||||
B O contido de molibdeno para o grao C90 tipo 1 non ten tolerancia mínima se o grosor da parede é inferior a 17,78 mm. | ||||||||||||||
C O contecto de carbono para R95 pode aumentar ata o 0,55% máximo se o produto está recollido por aceite. | ||||||||||||||
D O contido de molibdeno para T95 tipo 1 pode diminuír ata o 0,15% mínimo se o grosor da parede é inferior a 17,78 mm. | ||||||||||||||
E Para o grao EW P110, o contido de fósforo será do 0,020% máximo e o contido de xofre 0,010% máximo. |
Grao | Tipo | Elongación total baixo carga | Forza de rendemento | Resistencia á tracción | DurezaA, c | Grosor da parede especificada | Variación de dureza permitidab | ||
|
|
|
|
|
|
|
| ||
|
|
| min | máx |
| HRC | HBW | mm | HRC |
H40 | - | 0,5 | 276 | 552 | 414 | - | - | - | - |
J55 | - | 0,5 | 379 | 552 | 517 | - | - | - | - |
K55 | - | 0,5 | 379 | 552 | 655 | - | - | - | - |
N80 | 1 | 0,5 | 552 | 758 | 689 | - | - | - | - |
N80 | Q | 0,5 | 552 | 758 | 689 | - | - | - | - |
R95 | - | 0,5 | 655 | 758 | 724 | - | - | - | - |
L80 | 1 | 0,5 | 552 | 655 | 655 | 23.0 | 241.0 | - | - |
L80 | 9cr | 0,5 | 552 | 655 | 655 | 23.0 | 241.0 | - | - |
L80 | L3cr | 0,5 | 552 | 655 | 655 | 23.0 | 241.0 | - | - |
C90 | 1 | 0,5 | 621 | 724 | 689 | 25.4 | 255.0 | ≤12,70 | 3.0 |
12.71 a 19.04 | 4.0 | ||||||||
19.05 a 25.39 | 5.0 | ||||||||
≥25,4 | 6.0 | ||||||||
T95 | 1 | 0,5 | 655 | 758 | 724 | 25.4 | 255 | ≤12,70 | 3.0 |
12.71 a 19.04 | 4.0 | ||||||||
19.05 a 25.39 | 5.0 | ||||||||
≥25,4 | 6.0 | ||||||||
C110 | - | 0,7 | 758 | 828 | 793 | 30.0 | 286.0 | ≤12,70 | 3.0 |
12.71 a 19.04 | 4.0 | ||||||||
19.05 a 25.39 | 5.0 | ||||||||
≥25,4 | 6.0 | ||||||||
P110 | - | 0,6 | 758 | 965 | 862 | - | - | - | - |
P125 | 1 | 0,65 | 862 | 1034 | 931 | b | - | ≤12,70 | 3.0 |
12.71 a 19.04 | 4.0 | ||||||||
19.05 | 5.0 | ||||||||
aEn caso de disputa, as probas de dureza do laboratorio Rockwell C utilizaranse como método do árbitro. | |||||||||
bNon se especifican límites de dureza, pero a variación máxima está restrinxida como control de fabricación de acordo cos 7,8 e 7,9. | |||||||||
cPara probas de dureza a través da parede de graos L80 (todo tipo), C90, T95 e C110, os requisitos indicados na escala HRC son para o número máximo de dureza media. |
Ademais de garantir a composición química e as propiedades mecánicas, realízanse probas hidrostáticas unha por unha e realízanse probas de apagamento e aplanamento. . Ademais, hai certos requisitos para a microestrutura, o tamaño do gran e a capa de descarburización do tubo de aceiro acabado.
Proba de tracción:
1. Para o material de aceiro dos produtos, o fabricante debería realizar unha proba de tracción. Para o tubo soldado de Elecrtrice, dependentes na elección do fabricante, a proba de tracción pódese realizar na placa de aceiro que se usa para facer tubos ou perfomar o tubo de aceiro directamente. Unha proba realizada nun produto tamén se pode usar como proba do produto.
2. Os tubos de ensaio serán seleccionados aleatoriamente. Cando se requiran múltiples probas, o método de mostraxe asegurarase de que as mostras tomadas poidan representar o inicio e o final do ciclo de tratamento térmico (se procede) e os dous extremos do tubo. Cando se requiran múltiples probas, o patrón tomarase de diferentes tubos, excepto que a mostra de tubo engrosada pode ser tomada de ambos os extremos dun tubo.
3. A mostra de tubo sen fisuras pódese tomar en calquera posición da circunferencia do tubo; A mostra de tubos soldados debe tomarse a uns 90 ° á costura de soldadura ou a opción do fabricante. As mostras tómanse aproximadamente a cuarta parte do ancho da tira.
4. Non importa antes e despois do experimento, se a preparación da mostra é defectuosa ou hai unha falta de materiais irrelevantes para o propósito do experimento, a mostra pode ser despexada e substituída por outra mostra feita do mesmo tubo.
5. Se unha proba de tracción que representa un lote de produtos non cumpre os requisitos, o fabricante pode levar outros 3 tubos do mesmo lote de tubos para a súa reinspección.
Se todas as probas das mostras cumpren os requisitos, o lote de tubos está cualificado, excepto o tubo non cualificado que foi probado orixinalmente.
Se máis dunha mostra se mostra inicialmente ou unha ou varias mostras para a proba non cumpren os requisitos especificados, o fabricante pode inspeccionar o lote de tubos un por un.
O lote rexeitado de produtos pódese recalentar e reprocesar como un novo lote.
Proba de aplanamento :
1. O exemplar de proba será un anel de proba ou un corte final non inferior a 63,5 mm (2-1 / 2in).
2. Os exemplares pódense cortar antes do tratamento térmico, pero están suxeitos ao mesmo tratamento térmico que o tubo representado. Se se usa unha proba por lotes, tomaranse medidas para identificar a relación entre a mostra e o tubo de mostraxe. Debe esmagarse cada forno en cada lote.
3. O exemplar será aplanado entre dúas placas paralelas. En cada conxunto de exemplares de proba de aplanamento, unha soldadura foi aplanada a 90 ° e a outra aplanada a 0 °. O exemplar será aplanado ata que as paredes do tubo estean en contacto. Antes de que a distancia entre as placas paralelas sexa inferior ao valor especificado, non deberían aparecer rachaduras nin roturas en ningunha parte do patrón. Durante todo o proceso de aplanamento, non debería haber unha estrutura deficiente, soldaduras non fundidas, delaminación, exceso de metal ou extrusión de metais.
4. Non importa antes e despois do experimento, se a preparación da mostra é defectuosa ou hai unha falta de materiais irrelevantes para o propósito do experimento, a mostra pode ser despexada e substituída por outra mostra feita do mesmo tubo.
5. Se algunha mostra que representa un tubo non cumpre os requisitos especificados, o fabricante pode tomar unha mostra do mesmo extremo do tubo para probas complementarias ata que se cumpran os requisitos. Non obstante, a lonxitude do tubo acabado despois da mostraxe non debe ser inferior ao 80% da lonxitude orixinal. Se algunha mostra dun tubo que representa un lote de produtos non cumpre os requisitos especificados, o fabricante pode levar dous tubos adicionais do lote de produtos e cortar as mostras para volver a probar. Se os resultados destes retestos cumpren todos os requisitos, o lote de tubos está cualificado, excepto para o tubo seleccionado orixinalmente como mostra. Se algunha das mostras de proba non cumpre os requisitos especificados, o fabricante pode probar os tubos restantes do lote un por un. Á opción do fabricante, calquera lote de tubos pode volver a ser tratado e retroceder como un novo lote de tubos.
Proba de impacto:
1. Para tubos, tomarase un conxunto de mostras de cada lote (a menos que se demostre que se demostran que os procedementos documentados cumpren os requisitos regulamentarios). Se a orde está fixada en A10 (SR16), o experimento é obrigatorio.
2. Para a carcasa, deben tomarse 3 tubos de aceiro de cada lote para experimentos. Os tubos de ensaio serán seleccionados aleatoriamente e o método de mostraxe asegurarase de que as mostras fornecidas poidan representar o inicio e o final do ciclo de tratamento térmico e os extremos dianteiros e traseiros da manga durante o tratamento térmico.
3. Proba de impacto de Charpy V-Notch
4. Non importa antes e despois do experimento, se a preparación da mostra é defectuosa ou hai unha falta de materiais irrelevantes para o propósito do experimento, a mostra pode ser despexada e substituída por outra mostra feita do mesmo tubo. Os exemplares non deben ser simplemente xulgados defectuosos simplemente porque non cumpren os requisitos de enerxía mínimos absorbidos.
5. Se o resultado de máis dunha mostra é inferior ao requisito de enerxía absorbido mínimo, ou o resultado dunha mostra é inferior a 2/3 do requisito de enerxía mínimo especificado absorbido, tomaranse tres mostras adicionais da mesma peza e retomaranse. A enerxía de impacto de cada exemplar de novo será maior ou igual ao requisito de enerxía mínimo especificado absorbido.
6. Se os resultados dun determinado experimento non cumpren os requisitos e non se cumpren as condicións para o novo experimento, toman tres mostras adicionais de cada unha das outras tres pezas do lote. Se todas as condicións adicionais cumpren os requisitos, o lote está cualificado, excepto o que fallou inicialmente. Se máis dunha peza de inspección adicional non cumpre os requisitos, o fabricante pode optar por inspeccionar as pezas restantes do lote un por un, ou quentar o lote e inspeccionalo nun lote novo.
7. Se se rexeita máis dun dos tres elementos iniciais necesarios para demostrar que se rexeita un lote de cualificacións, non se permite que a reinspección demostre que o lote de tubos está cualificado. O fabricante pode optar por inspeccionar os lotes restantes peza a peza ou quentar o lote e inspeccionalo nun lote novo.
Proba hidrostática :
1. Cada tubo estará sometido a unha proba de presión hidrostática de todo o tubo despois do engrosamento (se é o caso) e o tratamento térmico final (se é o caso) e alcanzará a presión hidrostática especificada sen fugas. O tempo de mantemento da presión experimental foi composto por menos de 5 anos. Para tubos soldados, as soldaduras das tubaxes deberán comprobarse fugas a presión de proba. A non ser que a proba de tubos se realizase polo menos de antemán coa presión requirida para a condición final do extremo do tubo, a fábrica de procesamento de fíos debería realizar unha proba hidrostática (ou organizar tal proba) en toda a tubería.
2. As tubaxes a ser tratadas térmicas estarán sometidas a unha proba hidrostática despois do tratamento térmico final. A presión de proba de todos os tubos con extremos roscados debe ser polo menos a presión de proba de fíos e acoplamientos.
3. Despois de procesar ata o tamaño da tubaxe de extremo plano acabado e calquera articulación curta tratada térmicamente, a proba hidrostática realizarase despois do extremo plano ou do fío.
Diámetro do outter:
Alcance | Tolerane |
< 4-1/2 | ± 0,79 mm (± 0,031in) |
≥4-1/2 | +1%OD ~ -0,5%OD |
Para tubos de articulación engrosados cun tamaño menor ou igual a 5-1 / 2, as seguintes tolerancias aplícanse ao diámetro exterior do corpo do tubo a unha distancia de aproximadamente 127 mm (5,0 pulgadas) xunto á parte engrosada; As seguintes tolerancias aplícanse ao diámetro exterior do tubo a unha distancia de aproximadamente igual ao diámetro do tubo inmediatamente adxacente á porción engrosada.
Alcance | Tolerancia |
≤3-1/2 | +2.38mm ~ -0,79mm (+3/32in ~ -1/32in) |
> 3-1/2 ~ ≤5 | +2,78 mm ~ -0,75%OD (+7/64in ~ -0,75%OD) |
> 5 ~ ≤8 5/8 | +3,18mm ~ -0,75%OD (+1/8in ~ -0,75%OD) |
> 8 5/8 | +3,97mm ~ -0,75%OD (+5/32in ~ -0,75%OD) |
Para tubos espesados externos cun tamaño de 2-3 / 8 e maiores, as seguintes tolerancias aplícanse ao diámetro exterior da tubería que se engrosada e o grosor cambia gradualmente desde o final da tubería
Rang | Tolerancia |
≥2-3/8 ~ ≤3-1/2 | +2.38mm ~ -0,79mm (+3/32in ~ -1/32in) |
> 3-1/2 ~ ≤4 | +2,78mm ~ -0,79mm (+7/64in ~ -1/32in) |
> 4 | +2,78 mm ~ -0,75%OD (+7/64in ~ -0,75%OD) |
Grosor da parede :
A tolerancia ao grosor da parede especificada do tubo é -12,5%
Peso :
A seguinte táboa son os requisitos estándar de tolerancia ao peso. Cando o grosor mínimo especificado da parede é maior ou igual ao 90% do grosor da parede especificado, o límite superior da tolerancia masiva dunha única raíz debe aumentar ata o + 10%
Cantidade | Tolerancia |
Peza única | +6,5 ~ -3,5 |
Carga do vehículo Pesado de vehículos18144kg (40000lb) | -1,75% |
A carga do vehículo pesa < 18144kg (40000lb) | -3,5% |
Cantidade de pedido≥18144kg (40000lb) | -1,75% |
Cantidade de pedido < 18144kg (40000lb) | -3,5% |